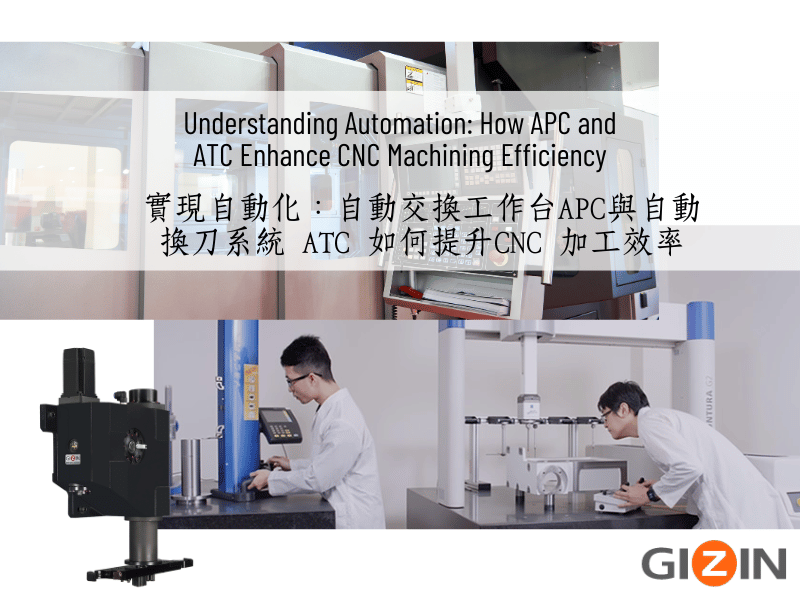
Understanding Automation: How APC and ATC Enhance CNC Machining Efficiency
Introduction
In the world of CNC machining, efficiency is key to meeting production demands and maintaining competitive advantages. Automation has transformed how we approach manufacturing, with technologies like Automatic Pallet Changers (APCs) and Automatic Tool Changers (ATCs) playing pivotal roles. Understanding how these systems work together can provide significant improvements in productivity, precision, and operational flexibility. In this article, we explore how APCs and ATCs enhance CNC machining efficiency.
The Role of Automatic Pallet Changers (APCs) in CNC Machining
Automatic Pallet Changers are designed to reduce machine downtime by enabling rapid workpiece exchange. By pre-loading workpieces on pallets, APCs allow CNC machines to continue operations without waiting for manual setup or changeovers.
Key Benefits of APCs:
- Minimized Downtime: APCs allow for quick swapping of workpieces, ensuring that the spindle remains engaged in machining operations with minimal interruption.
- Improved Workflow: While one workpiece is being machined, another can be set up on a separate pallet, optimizing the operator’s time and workflow.
- Enhanced Flexibility: APCs support high-mix, low-volume production by simplifying the changeover process, making it easier to switch between different parts or jobs.
Applications of APCs:
- Mass Production: Ideal for automotive and aerospace industries where large batches of identical parts are required.
- Custom Manufacturing: Useful for job shops that handle varied projects, allowing quick changeovers between custom parts.
The Importance of Automatic Tool Changers (ATCs)
Automatic Tool Changers are crucial for multi-step machining processes, allowing machines to switch tools automatically without manual intervention. This capability is essential for complex parts that require multiple machining operations.
Key Benefits of ATCs:
- Increased Efficiency: ATCs reduce the time needed for tool changes, enabling continuous production and minimizing idle spindle time.
- Precision and Consistency: Automated tool changes ensure that each tool is positioned accurately, maintaining high precision throughout the machining process.
- Tool Management: ATCs facilitate organized tool storage and quick access, reducing the chances of tool misplacement or damage.
Applications of ATCs:
- Precision Engineering: Essential for industries like medical device manufacturing, where multiple precise operations are required on a single workpiece.
- High-Volume Production: Suitable for automotive parts production, where rapid and repetitive tool changes are necessary.
Synergy Between APC and ATC
When integrated, APCs and ATCs create a highly efficient and automated machining environment. Here’s how they work together:
- Continuous Operation: While the APC swaps out workpieces, the ATC prepares the necessary tools for the next operation, ensuring no time is wasted.
- Reduced Setup Times: With pre-loaded pallets and pre-configured tools, setup times are drastically reduced, allowing for quicker transitions between jobs.
- Enhanced Precision and Productivity: By automating workpiece and tool handling, manufacturers can maintain consistent quality and higher throughput.
Implementing APC and ATC for Maximum Efficiency
To maximize the benefits of APC and ATC systems, consider the following:
- Assess Production Needs: Understand the volume, variety, and complexity of parts being produced to determine the optimal APC and ATC configurations.
- Invest in Quality Components: High-quality APCs and ATCs are critical for reliable performance and long-term efficiency.
- Regular Maintenance: Ensure both systems are regularly inspected and maintained to prevent unexpected downtime and prolong equipment life.
Conclusion
Integrating Automatic Pallet Changers and Automatic Tool Changers into CNC machining operations can dramatically enhance efficiency, precision, and flexibility. By automating workpiece and tool handling, these systems reduce downtime, improve workflow, and allow manufacturers to meet demanding production schedules with ease.
At GIZIN, we specialize in providing high-quality ATC Camboxes designed to seamlessly integrate with APC systems, optimizing CNC machining processes. Our solutions are engineered to deliver superior performance, enabling you to achieve maximum productivity and precision.
Call to Action
If you're ready to enhance your CNC machining efficiency with APC and ATC solutions, or need expert advice on selecting the right systems for your operations, contact GIZIN today. Let us help you drive productivity and maintain a competitive edge in your industry.